Sustainability begins with an open mind for changes
In our factories, we have a change management team that constantly looks after improvements and more efficient and productive ways of working. At Viessmann we call our change management philosophy VITOTOP.
Once a year, an internal VITOTOP audit, according to our company values responsible, team-oriented and entrepreneurial, takes place to keep the minds of employees and managers focused on sustainable work routines and clear processes.
Constant examination of processes for the seven types of losses
This principle helps us to be more efficient and productive and at the same time reduce waste and avoid emissions. Running machines only at the necessary level for operation saves resources and prevents waste.
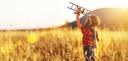
Protection of the resource people
Our employees are helping us every day to succeed as one team. So, they are our most valuable resource. Therefore, we try to design the working environment as ergonomic, safe and healthy as possible. For example at our foaming machines we introduced so-called shuttles to avoid heavy lifting for our employees.
Quality improvement and error prevention with Poka Yoke
Poka Yoke aims to avoid the occurrence of an error or its propagation by checking all parts. This is the principle that we follow, for example, in our material supply in our production process. We provide all necessary parts for one product in a certain box, to minimize the probability that any element is forgotten during manufacturing of that product.
Visualisation of processes for transparent communication
We use different tools to ensure that all employees understand our standard processes and maintain the same quality for every process and product. Standard sheets, value stream design, and value stream analysis are some of the tools we use to communicate transparently, explain things quickly and visually and avoid misunderstandings.
Total productive maintenance (TPM) to maintain and improve standards
TPM is about routine maintenance measures that can be carried out independently by the production staff. At Viessmann, we have defined 3 TPM levels with regard to basic inspection, methods and improvement. Specific cleaning, inspection and maintenance checkpoints are therefore visualised and displayed on a TPM board at the plant. This is how we systematically verify that the current standard is being maintained and to strive for continuous improvement.